Contents
IoT 導入の背景
既存の工場設備をIoTで効率的に運用したい
トーア紡コーポレーションは、前身は1922年の創業、羊毛紡績から始まった100年近い歴史がある素材メーカーです。世界品質の毛糸から生地、スーツなどの衣料を手掛けるほか、紡績で培ったノウハウを活かしてインテリア産業資材事業、さらにはファインケミカル事業、アプライアンス事業、不動産事業など多角的な事業を展開しています。
トーア紡コーポレーションは、関連会社も含めると全国に多くの工場を持っています。「工場のデジタル化」は、FA機器でのPLC導入などで進めてきました。しかし、工場の設備は、大きな初期コストが掛かるため、頻繁に最新鋭の設備に変えられない状況があります。
本社で情報システム部長を務める中井氏は、ある展示会で「最近のIoTは、既存の設備を変えずに安価に導入可能である」と耳にしました。そこで、現場にIoT活用のニーズについてヒアリングを重ね、トーア紡マテリアル(インテリア産業資材事業)で「工場の電力の見える化」に取り組むことになりました。
IoT 導入の課題
工場の電力消費をリアルタイム見える化、夏のピーク抑制に成功
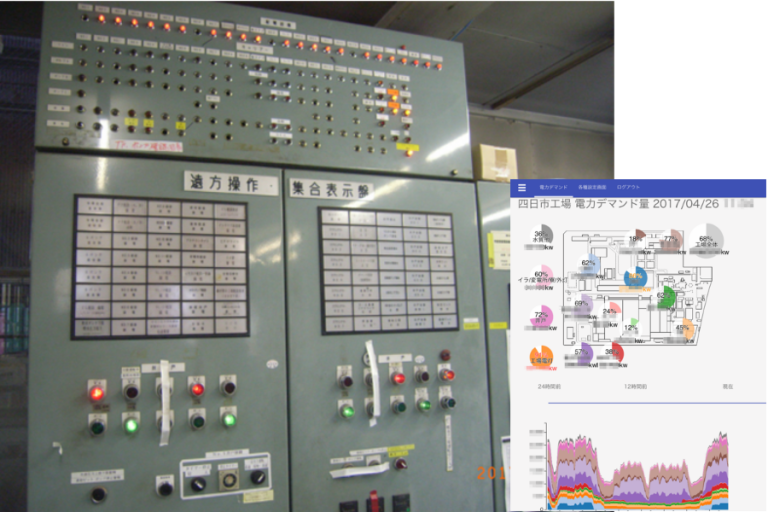
工場では、電力会社とオンデマンド契約(過去1年間の最大需要電力から契約電力を決定する)を結びます。契約上限を超えないよう、電力利用抑制や一時的な発電機利用を通じて電力利用を管理します。以前は、PLCから工場装置の電力利用量のデータを取得し監視センターで管理していましたが、夏場など頻繁にピークを検知する時期は、管理員不足が発生していました。そこで「電力利用量データを、誰でもチェックできる」仕組みを検討しました。
IoT化には3つの課題がありました。まず「PLCデータの変換」です。PLCが持つデータ形式はインターネットに連携できません。そこで、SPSインテグレーションパートナーのIoT.kyoto(株式会社KYOSO)の協力を得て、PLCにレジスタ上のデータを一定間隔でCSV出力するオプション機器を追加し、Linuxゲートウェイで受けてクラウドへ送信する構成にすることで、既存設備の設定を一切変えることなくデータ取得する仕組みを開発しました。次に「ネットワーク」です。この点はLinuxゲートウェイにSORACOM IoT SIMを用い、セルラー回線を利用しています。最後に「データの見える化」です。KYOSO社が提供するサービス「IoT.kyoto.IVS」で、電力利用データを工場内のモニタおよび作業員のスマートフォンで見える化、アラート通知しています。
こうして電力利用の見える化が実現しました。2ヶ月の構想と、1週間の設置で2016年夏から開始、その夏のピーク抑制で成果を上げました。翌年2017年夏は、エリア毎の電力ピークの管理を実現、さらなる改善効果を得ています。
SORACOMが選ばれた理由
セルラー通信の活用で現場のやり方や設備を変えずにIoT導入が可能に
工場設備は構内LANにつながっており、インターネットにデータを送信できません。新たにネットワークを敷設する場合も、既存の設備やオペレーションを邪魔しないように天井や壁などにネットワーク配線をする必要があり、時間もコストも掛かります。
「ネットワーク敷設には契約や業者の手配などに数週間かかり、コストも数百万近くかかります。しかし、SORACOMのセルラー通信と外付けの通信機器を用いれば数万円、当初の1/10程度です。このコストでできるなら『やる』しか選択肢がありません」(中井氏)
さらにセルラー通信の利用によってスムーズにIoTを導入できたと中井氏は言います。「実稼働している工場は止めることができません。初めからオペレーションを変えることを前提に、IoT活用、データ取得を導入しようとすると現場は困惑してしまいます。まずは今の設備やオペレーションを変えずに始めることで、現場の理解を得やすくなります。」(中井氏)
システム構成図
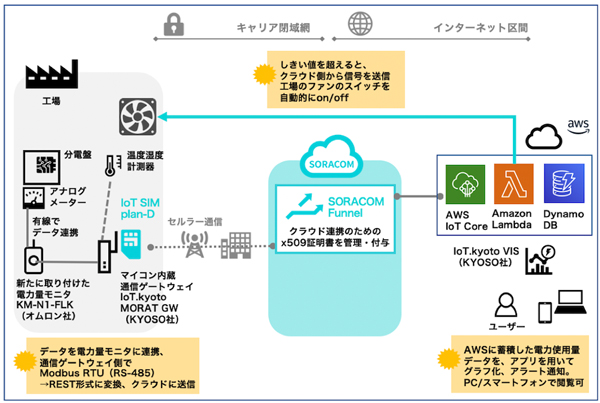
導入の効果
古い設備のIoT化に着手、電力監視、温度湿度管理と空調の自動制御を実現
2019年に、東亜紡織(衣料素材事業)の毛糸製造を行う宮崎工場のIoT化に着手しました。宮崎工場の工場設備はPLCもなく、古いアナログメーターを目視、手書きのデータ記録と設備に付随した警報装置で電力を監視していたため、データ化からの出発でした。試行錯誤の後、アナログメーターと同じ電力系統にModbus RTU/CTクランプ対応の電力量モニタを設置、Modbus RTUでデータを取得してからクラウドに連携する方法を取ることにしました。この仕組みで、工場内の配電盤から電力利用量データを取得、作業員は手元のスマートフォンでリアルタイムでデータ閲覧できています。
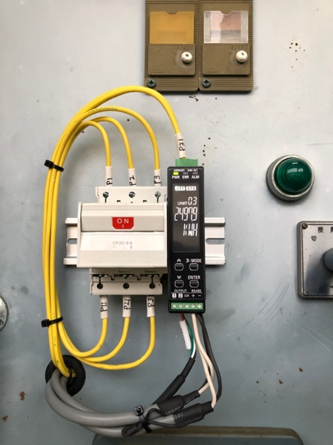
その後、工場内の空調管理に取り組みました。近代紡績では、毛糸製造には良質な羊毛と、温度湿度の最適化が品質向上の鍵です。当時、工場内の温度湿度の計測器とそれらを管理する熟練作業員のノウハウで空調を管理している状況でした。そこで、EnOceanを用いた電源不要の温度湿度センサーで工場の設備周辺の温度湿度を計測し、SORACOMのSIMを設定した通信ゲートウェイに連携、クラウドに送信します。さらに、ある一定の条件でクラウド側から工場内の空調装置に信号を送りON/OFFを自動制御します。
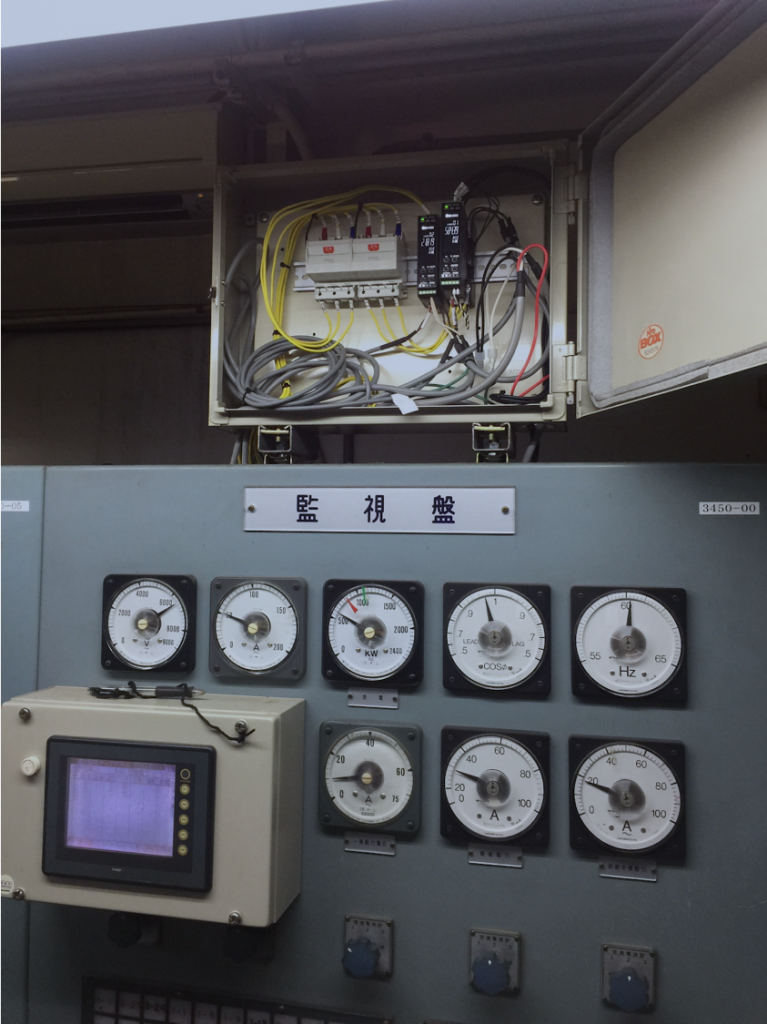
この仕組みにより、電力利用量の推移、各エリアの温度湿度の推移がデータ化され、熟練作業員のノウハウがデータ化され始めています。次のステップとして、製造工程上での障害発生時間帯のデータ化を検討しており、今取得しているデータを組み合わせて不良品発生の予測に役立てようと考えています。
今後の展開について
最新技術を活用して既存のオペレーションを刷新することもDX
電気や機械を扱う現場にとってITは未知の世界、現場からIT部門に相談が来ることはまずないと中井氏は言います。中井氏は自ら現場に行き、実作業を見ながら「これを毎日やるのは大変じゃないですか」「この管理はITで便利にできそう」と一緒にアイディアを出すそうです。「現場に行くことが大事」と中井氏はIoT活用を振り返ります。
「100年前会社を起こした先人は、海外の最先端の手法を学び取り入れたはずです。その後オペレーションは日々現場で改善されてきましたが、古い工場設備においては最新のやり方は導入できないと考え、人手に頼ってきたオペレーションもあります。既存のオペレーションを最新技術で進化させることはDXの入り口です。工場の様々なデータがデジタル化されることで、データ分析や予兆検知などの次のステップに進めます」(中井氏)
工場の新しい改善活動は、今まで培われたノウハウや技術とともに「考える力」を現場に改めて根付かせ、若手を含めた組織成長、活性化という目に見える形で現場に浸透し始めているということです。
目次
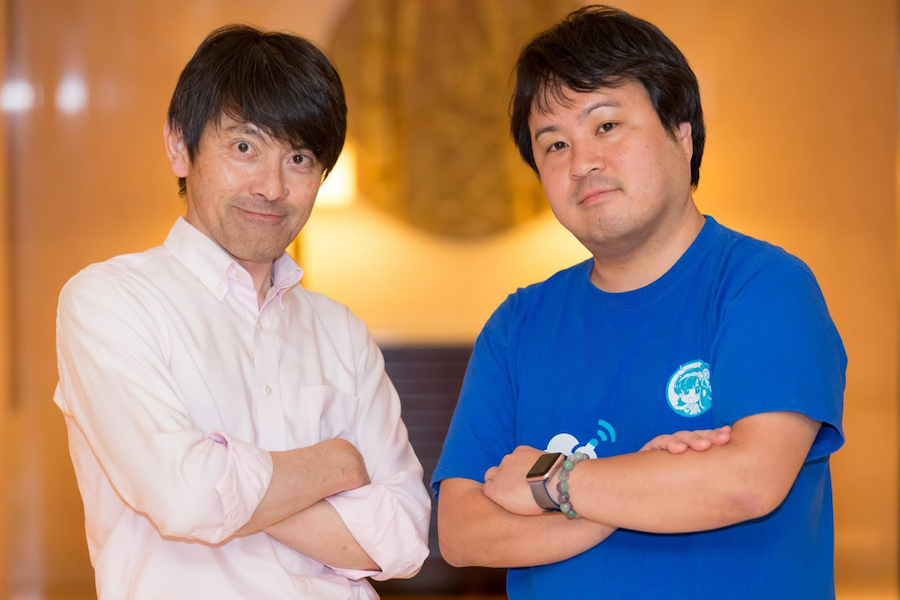
株式会社トーア紡コーポレーション
IT推進部 部長
中井 邦義氏(写真左)
株式会社KYOSO
IoT.kyoto シニアエバンジェリスト 辻 一郎氏(写真右)
DOWNLOAD
導入事例ダウンロード
さまざまな業界のSORACOMを利用した最新IoT事例集をダウンロード頂けます。
下記フォームを入力いただき、送信ボタンを押してください。
全て必須項目となります
個人情報の取り扱いについては、
お客様の個人情報に関するプライバシーポリシーをご確認ください。